Exactly how to Create a Reliable Welding WPS: Tips and Ideal Practices
Exactly how to Create a Reliable Welding WPS: Tips and Ideal Practices
Blog Article
Opening the Power of Welding WPS: Strategies for Efficiency and Safety And Security in Manufacture
In the world of fabrication, Welding Treatment Requirements (WPS) stand as the foundation of welding operations, dictating the needed actions for achieving both performance and safety and security in the fabrication process. Understanding the ins and outs of WPS is extremely important to harnessing its complete possibility, yet many organizations struggle to open real power that lies within these papers (welding WPS). By delving into the strategies that maximize welding WPS, a globe of improved productivity and increased safety and security waits for those happy to check out the nuances of this important facet of manufacture

Significance of Welding WPS
The importance of Welding Treatment Specifications (WPS) in the fabrication industry can not be overemphasized. WPS function as a vital roadmap that outlines the required steps to guarantee welds are performed consistently and correctly. By defining vital criteria such as welding processes, materials, joint designs, preheat temperatures, interpass temperature levels, filler metals, and post-weld warmth therapy requirements, WPS supply a standardized technique to welding that improves performance, top quality, and safety in manufacture processes.
Adherence to WPS aids in attaining uniformity in weld top quality, minimizing the chance of issues or structural failures. This standardization likewise assists in compliance with industry regulations and codes, ensuring that produced structures satisfy the required safety standards. Additionally, WPS paperwork allows welders to duplicate successful welding procedures, causing regular results throughout various projects.
Fundamentally, the precise advancement and strict adherence to Welding Procedure Specifications are extremely important for upholding the stability of bonded frameworks, safeguarding against potential dangers, and supporting the credibility of construction companies for providing premium product or services.
Crucial Element of Welding WPS
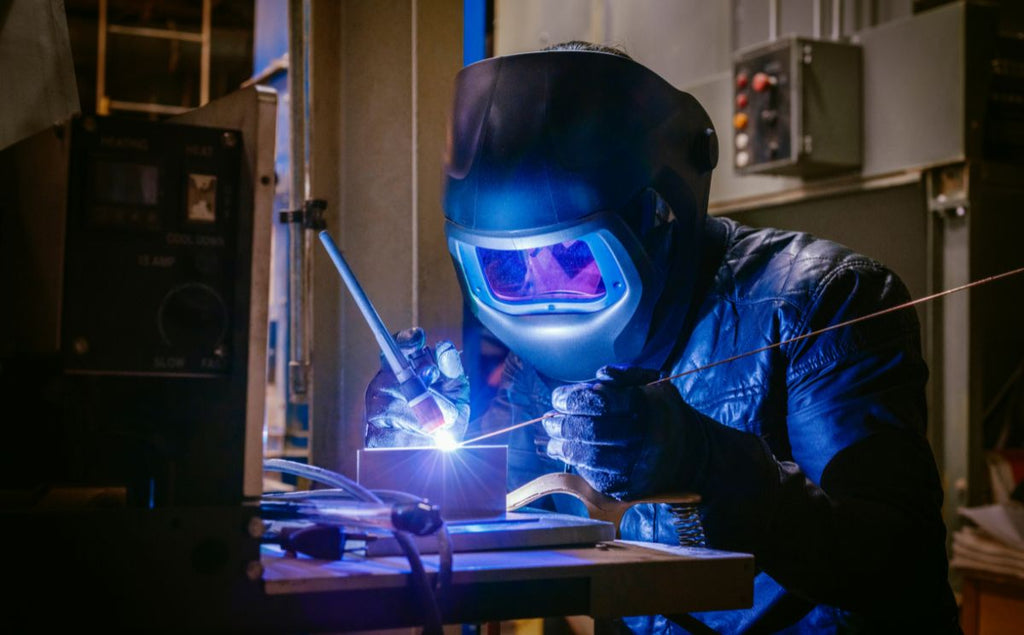
Enhancing Effectiveness With WPS
When optimizing welding procedures, leveraging the crucial elements described in Welding Treatment Specs (WPS) becomes vital for enhancing processes and taking full advantage of performance. One method to improve efficiency with WPS is by meticulously picking the suitable welding specifications. By sticking to the certain guidelines offered in the WPS, welders can make certain that the welding devices is established up properly, leading to premium and regular welds. Furthermore, following the pre-approved welding series described in the WPS can dramatically reduce the time invested in each weld, eventually boosting general efficiency.
Furthermore, appropriate training and accreditation of welders in understanding and executing WPS can better boost effectiveness. Ensuring that all staff member are skilled in analyzing and carrying out the WPS accurately can rework and decrease mistakes, saving both time and sources. Consistently assessing and updating the WPS to incorporate any type of lessons discovered or technological improvements can additionally add to efficiency improvements in welding procedures. By embracing the standards stated in the WPS and continually seeking means to maximize procedures, makers can accomplish greater performance degrees and superior end results.
Ensuring Security in Construction

Security procedures in manufacture play a pivotal function in securing workers and enhancing functional treatments. Ensuring security in fabrication involves a multifaceted approach that includes numerous elements of the welding procedure. One basic aspect is the arrangement of individual safety devices (PPE) customized view to the other specific threats present in the construction environment. Welders need to be outfitted with suitable gear such as headgears, handwear covers, and safety clothes to mitigate risks connected with welding tasks.
Additionally, adherence to appropriate air flow and fume extraction systems is essential in maintaining a healthy and balanced job setting. Welding fumes have unsafe materials that, if breathed in, can pose severe health threats. Applying effective air flow procedures aids to reduce direct exposure to these unsafe fumes, promoting respiratory wellness among workers.
Normal devices upkeep and assessments are also necessary for making certain safety in fabrication. Faulty equipment can lead to crashes and injuries, emphasizing the value of timely fixings and routine checks. By prioritizing precaution and promoting a culture of recognition, construction facilities can create a efficient and safe and secure job setting for their personnel.
Applying WPS Ideal Practices
To boost functional effectiveness and guarantee high quality outcomes in construction processes, integrating Welding Treatment Specification (WPS) finest techniques is extremely important. Selecting the suitable welding procedure, filler material, and preheat temperature specified in the WPS is essential for achieving the desired weld top quality. Making sure that qualified welders with the necessary qualifications bring out the welding treatments according to the WPS standards is essential for uniformity and dependability.
Final Thought
In verdict, welding WPS plays a vital role in guaranteeing efficiency and safety in manufacture processes. By complying with these strategies, organizations can open the full potential of welding WPS in their fabrication procedures.
In the world of manufacture, Welding Procedure Specs (WPS) pop over to this site stand as the backbone of welding procedures, determining the necessary actions for attaining both effectiveness and safety and security in the construction process. By defining essential parameters such as welding processes, products, joint layouts, preheat temperature levels, interpass temperatures, filler steels, and post-weld warm therapy demands, WPS give a standardized strategy to welding that improves effectiveness, high quality, and safety in manufacture processes.

When enhancing welding procedures, leveraging the vital components outlined in Welding Procedure Specs (WPS) ends up being vital for improving processes and making the most of efficiency. (welding WPS)
Report this page